3.5.2Health, Safety and Security
Our ApproacH
Acknowledging the nature of the business, SBM Offshore has implemented the Sustainability Policy. SBM Offshore is committed to fostering an injury-free work environment for all the workforce, including employees, contractors, and subcontractors, by managing risks and critical controls at all organizational levels.
SBM Offshore has established a Management System Assurance framework that adheres to the standards for which the Organization is certified (for more details see section 3.8.5 – Certification table). This framework relies primarily on internal assessments and audits conducted by qualified personnel to review the suitability of processes and their implementation and execution.
SBM Offshore is committed to an ongoing journey toward ’Target Excellence’, focusing on the core objectives of No Harm, No Defects and No Leaks. This ambition enables the safeguarding of people and assets, while managing the impacts on the environment and climate change. SBM Offshore strengthens this commitment through the annual LIFE DAY, which celebrates and protects life across all areas of SBM Offshore. Moreover, all personnel have both the right, and the duty, to stop work in the event that business activities are conducted in violation of the Sustainability Policy, to reinforce the collective responsibility for safety.
The approach to managing potential health and safety hazards, along with their associated controls and safeguards, is based on a lifecycle hazard management process integrated within GEMS. The hazard management process applies to all SBM Offshore projects and begins with hazard identification. Following this, SBM Offshore implements actions aimed at eliminating hazards. When elimination is not reasonably practicable, risks are reduced to acceptable levels, in accordance with the hierarchy of controls methodology. Closing the cycle, monitoring, reviewing and recording of the lessons learned are performed. SBM Offshore delivers specialized training to ensure process effectiveness.
Considering the fragmentation of the modern world, with constant evolving threats affecting both national and regional security, SBM Offshore is highly committed to ensuring the security of personnel and assets. In 2024, SBM Offshore developed specific security risk assessments for new projects located in high-risk areas or countries, such as Nigeria and Mexico. Different security rules have been drafted and security set-ups have been implemented, depending on the location of these projects, to ensure the safety and security of the workforce traveling to those areas.
Promoting and supporting employee health and well-being is central, reflecting one of SBM Offshore’s core values: 'Care’. At SBM Offshore, Health and Well-being is managed as a Group function, directly reporting to the Group HSSEQS Director. This structure ensures that health and well-being are integrated into daily operations and organizational culture.
Performance
SBM Offshore assesses company HSSE performance through a set of indicators. Those indicators are established, based upon energy sector benchmarks and internal critical analysis. Operations and Projects Management teams contribute to the target definitions, based on the previous years performance and a continuous improvement approach. The targets are approved by the SBM Offshore Management Board. As part of the Target Excellence ambitions, SBM Offshore has the objective to be among the 10% of best performing IOGP members in Occupational and Process Safety results by 2030.
Seeking excellence in occupational and process safety, SBM Offshore has changed the approach related to serious incidents management, adopting IOGP methodology for Fatalities and Permanent Impairment (FPI) injuries prevention. The internal procedures and KPIs have been updated and a new metric has been established, which will focus the organization on achieving zero FPI. TRIFR targets are used as a guide for minimum and maximum scores to ensure zero FPI. This is aligned with the industry approach and focus. In line with this change, SBM Offshore will keep tracking TRIFR, but no longer as a target. Instead, a ceiling has been established to be used as reference to compare with benchmarks. It is a way to push for effective reduction on recordable incidents, while keeping and enhancing the reporting culture.
Monthly reports and critical analysis are performed and shared to track the results and assess the HSSE programs´ effectiveness. Critical analysis promotes corrective actions whenever they are needed. HSSE campaigns and promotions are implemented in order to support business units to achieve the expected results.
The following table provides the targets set for 2024 and the performance achieved:
| 2024 Target | 2024 Performance | Details |
---|---|---|---|
Total Recordable Injury Frequency Rate (TRIFR) | <0.10 | 0.101 | section 3.9 |
Fatalities and Permanent Impairments (FPI) | 0 | 01 | section 3.9 |
Tier 1 PSE with more than 3 severity weight points as per API 754 | < or equal to 2 | 1 | section 3.9 |
Occupational Illness Frequency Rate (OIFR)2 | na | 0.204 | section 3.9 |
Security incidents | na | 11 | na |
- 1 In November 2023 a fatality happened on FPSO Kikeh. A note was added in 2023 annual report once by the time the report was issued the investigation was not concluded. The incident investigation was concluded in 2024 resulting in a non-work related fatality.
- 2 For employees.
In 2024, SBM Offshore further expanded its HSSE and Process Safety initiatives:
Health
- Maintained and enhanced the Well-being Matters Program, which addresses presenteeism, work-life balance, job stressors, workplace injuries and illnesses. This program provides comprehensive and holistic support to employees in their social, physical and emotional health, incorporating occupational health services and company guidelines. More than 40% of the target audience have participated in the online training about mental health offered in 2024.
- Each SBM Offshore location has established well-being champions with certified training to support those experiencing a mental health challenge, to raise awareness about mental well-being, to help recognize signs of concern and explore how to intervene and manage a conversation in an effective way. A total of 13 champions were active in 2024.
- e-Learning courses in fatigue management and mental health awareness were developed and made available for employees. Almost 53% of total population attended the Fatigue Management e-Learning and 50%, the Mental Health Awareness.
Safety
- Implemented the IOGP methodology for FPI injuries, replacing the previous Serious Injuries and Fatalities program. This alignment ensures that SBM Offshore adheres to best practices within the oil and gas sector.
- Implemented a global standard for Human Factors and Performance, alongside initiatives to ensure its integration at all levels of SBM Offshore. This approach aims to cultivate a psychologically safe environment that effectively addresses the human interface with work processes.
- Actively participated in the improvement of industry standards through IOGP work groups focused on FPI and the Human Performance Subcommittee.
- Ensured compliance with certification requirements for both onshore bases and offshore units.
The following graph illustrates that SBM Offshore’s TRIFR has consistently remained below the average of the IOGP since 2018. This achievement is a key component of SBM Offshore’s commitment to being in the top 10% of the IOGP benchmark by 2030.
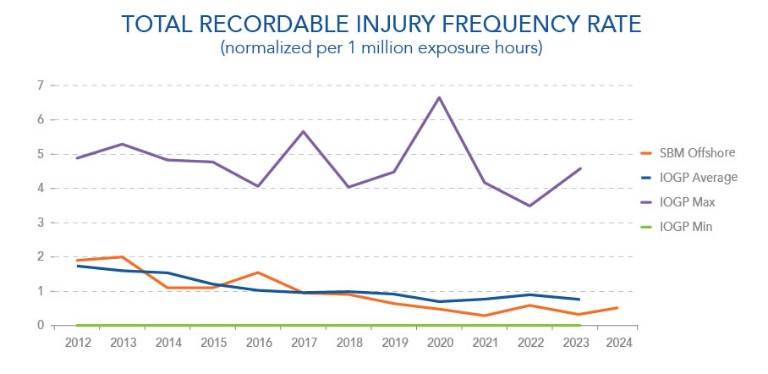
Security
- Risk assessments for new projects in high-risk areas or countries, such as Nigeria and Mexico.
- Specific security rules according to location characteristics: SBM Offshore established specific security induction for its employees, according to the country where they are assigned to work.
Process Safety
- Implemented the Group Performance Standard process review, ensuring that appropriate metrics and controls are in place for process safety in relation to SBM Offshore’s inherent process hazards.
- Continued to uphold the Hazards and Effects Management Process (HEMP) by effectively managing the risks associated with Major Accident Hazards (MAHs) and their potential Major Accident Events (MAEs).
The quantity of oil discharged to sea per hydrocarbon production was 3.73 tonnes per million tonnes of hydrocarbon produced, 61% below the IOGP benchmark (2022) and no oil spills above 1 barrel (as per IOGP definition). SBM Offshore is committed to achieving a higher environmental performance compared with the 2023 IOGP industry benchmark for oil spills per unit of production, as well as 50% improvement over the 2023 benchmark for oil produced in water.
future
SBM Offshore has defined the following 2025 targets:
- Zero Fatality or Permanent Impairment Injury.
- TRIFR Ceiling: 0.10.
- Number of PSE Tier 1: Zero event with more than 3 severity points as per API 754 classification.
SBM Offshore has planned the following key initiatives for 2025, based on critical analysis and a continuous improvement approach:
- Enhance the Target Excellence Program, increasing visibility of strategic objectives and adherence throughout the organization (No Harm. No Defect. No Leak).
- Progress in occupational safety with the FPI prevention program and its related initiatives.
- Assure human factors and performance principles are embedded in the management system and fully implemented across the organization.
- Maintain security controls on SBM Offshore’s activities: continually driving improvements on procedures and practices to maintain thorough security controls on its activities.
- Maintain compliance with certification requirements on shorebases and offshore units.
- Continue increasing health and wellbeing awareness, training and related programs.
- Improvement actions for employee mental health and wellbeing:
- Enhance country specific Well-being Matters program.
- Maintain and enhance SBM Offshore’s medical surveillance program for better health and well-being for all (SDG3).
- Keep developing and enhancing the process safety management framework by implementing the Group performance standards for Safety and Environmental Critical Equipment (SECE).
- Keep and enhance Life Day in all projects, operations and offices.